Of Blind Bolts and Radius Rod Mounts
Lookin for Another Way
Mounting the ends of radius rods, especially split wishbones, simply shouldnt be that difficult, right? After all, about a bazillion open-wheel cars have been built and the radius rod mounts have been pretty much the same: you cut the eye (the piece with that uniquely-Ford tapered hole) off a steering arm or two, weld it to a piece of steel plate and bolt that plate to the side rail of your car and youre done. End of conversation.
So, why is everything I do so damn difficult and different?
When it came time to mount my radius rods I discovered three things that I knew were going to give me more than my share of heartburn.
-my radius rods terminated right at my firewall line and since the body was channeled over the frame, the frame wasnt visible to bolt to. This wouldnt be a big deal except those carefully crafted panels Id put on the bottom of the body snugged right up against the frame rail. I COULDNT BOLT TO THE OUTSIDE OF THE RAIL BECAUSE THERE WASNT ROOM.
I couldnt bolt through the frame anyway because there wasnt room for the bolt heads.
-On the left rail the steering box and all of its bolts and doublers were right where Id want to put the radius rod mounts.
I considered shortening the radius rods, but I felt as if they were short enough already. Besides, conventional wisdom today says you arent supposed to use radius rods on a tube axle because the tube wont twist like an I-beam axle will on bumps and something is bound to break. Youre supposed to use four-bars. Shortening the radius rods would amplify the problems.
Of course, during the 50s we werent smart enough to know all of the above, but I dont remember anything breaking. In fact, if you look at the Bill Niekamp, Worlds Most Beautiful Roadster (a kick-ass, track nosed 29 roadster) youll see radius rods on a tube axle. If you look at almost all midgets and sprints of the period, youll see radius rods on tube axles. So Im not worried about my set up. If I can ever get it to work, that is.
My first thought about mounting the radius rod perches was to run six inch bolts vertically through the 4 tubing rails, but that wouldnt work on the left side because of the steering box and its bolts. Besides, those are awfully long bolts and would eventually work loose.
My second throught was to cut holes on the inside of the frame rail that would let me put nuts inside the frame rails for the bolts. But that wouldnt work on the left side. Besides, it went against the grain to cut weakening holes just to gain access to a couple of nuts.
The solution popped up while I was mounting the steering box. One of its bolts had no room for a nut on the outside because of body interference. So I came up with the how-to-put-a-nut-inside-a-frame-without-cutting-a-big-whopping-hole system. If you look at the pictures youll see how it works.
For the radius rod mounts, themselves, I welded up L shaped brackets out of 3/16 4130 (just because I had it). I carefully measured (and re-measured) the wheelbase on both sides of the car, measured a bunch of diagonals and marked the frame rails for the proper locations of the brackets. I drilled 1/4 holes in the base of the right bracket, then lightly tack welded it in place on the rail. I didn't want it to move. Then I match drilled 7/16 holes through the bracket and the frame rail at the same time. That way I knew the holes exactly matched.
Then I drilled 7/16 holes in the top of the rail in a matching position.
The goal of the next operation was to put Grade 8 nuts on the inside of the bottom of the frame rail in such a way that theyd always be there and I wouldnt have to worry about them moving.
Take a look at the pix. Personally, I think the concept works slicker n a squashed gopher, as we used to say back in Nebraska.
First I took 3/4" pieces of steel tubing (pipe would work) and bored 1/2" holes in the end to let the bolt pass through the nut, which I was going to weld to the end of the tube. The tubes were slightly longer than the rails were deep - 4" plus.
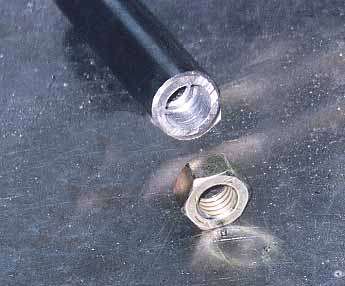 |
I bought a 3/4" bit ($27 (!) if you can believe it!) and opened the holes in the top of the frame out to 3/4"
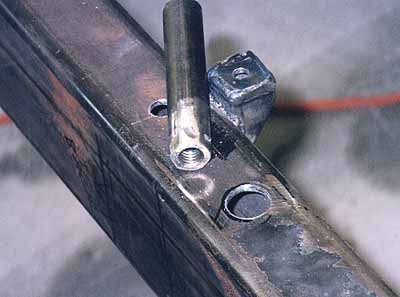 |
I chamfered the end of the tubing heavily and pounded a short piece of 3/8" steel rod into the end to be welded over. I made sure the surface of the tube was slightly below the surface of the rail so I wouldn't have to worry about grinding off all of the weld. When I put the tube through the hole, I inserted a bolt from below and pulled the nut as tight as I could to the inside, bottom of the frame rail.
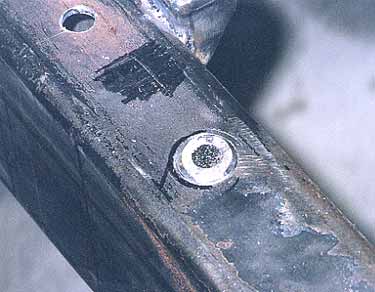 |
When I was finished fitting everything, I welded the tubing in place then continued running enough wire into the recess that I could grind it flush. Some primer, a little glazing putty and you'll never know it was there.
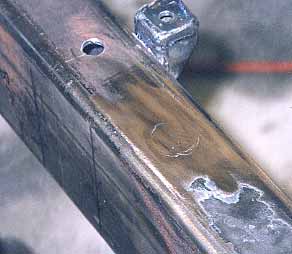 |
This is the way the bottom right radius rod mount looks bolted in place. Cool, huh?
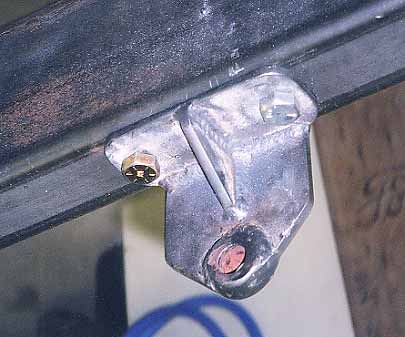 |
The left mount took an entirely different approach because of all the steering box stuff taking place right in the area. I match drilled holes from the bracket to a piece of 1/2" cold roll plate. Then I tapped those holes for 7/16 threads. I heavily chamfered the edges of the 1/2" block and welded it to the frame rail. The bracket bolts to that.
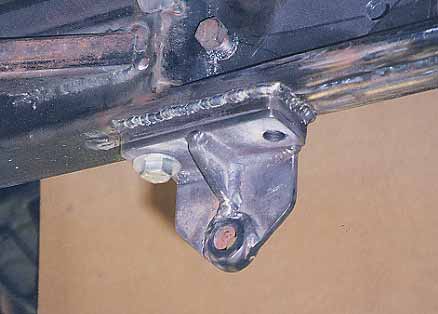 |
As is always the case, I spent more time worrying and thinking about the project then actually doing it.
I think this works really well.